Capiz Sugar Central, Inc. |
Material and Spare Parts Acquisition and Inventory Control System |
"I saved well over 100 days of development time using Iron Speed Designer."
- Jaime Jegonia, Owner of JimiTron Software
|
|
|
Material and Spare Parts Acquisition and Inventory Control System |
Capiz Sugar Central, Inc.
Capiz, Philippines
|
The Material and Spare Parts Acquisition and Inventory Control System was developed for
Capiz Sugar Central, Inc. of Capiz, Philippines. Capiz is the second-largest sugar cane
miller in this region with over 420 employees, and this application is used by all of their
office personnel.
This application processes a variety of different business transactions, including: Requests
to Purchase (RTP), Quotations, Budget Checking, Purchase Orders, Receiving Reports, Accounts
Payable, and Stock Requisition Slips. It also handles all Warehouse Issue Requests (WIR) in
dynamic real-time. The Inventory Control System has a paperless validation and approval schema
and the inventory counts are maintained in master files and can be traced back to item-by-user
departments.
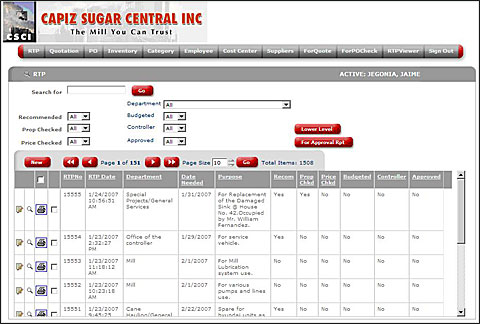
Page contents are restricted by user as a result of the 10-level multi-role security feature.
When an employee requests material, he logs into the program and checks availability through
the Inventory master control. From there, the employee opens a new Request to Purchase and adds
additional materials if needed. Once the request is initiated, the application automatically selects
the recommended canvasser, warehouseman, purchaser, budget officer, controller, and final approving
officer. It also auto-populates the current date, delivery date, and requesting department.
Additionally, the application filters all materials associated with the user and any items
that are common to all departments.
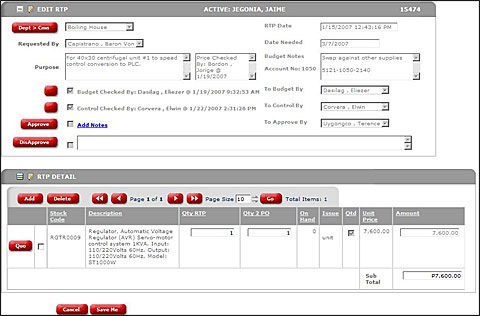
Users can select active buttons and enabled fields to complete a transaction.
Once the RTP is initiated, only the requester can edit a recommendation prior to its approval.
From this point, the document is ready for the second approval, prompting an activation button
to appear in the RTP. Once approved by the overseeing officer, the button disappears and the RTP
continues to the next officer until final sign-off is obtained. All completed documents are available
for viewing and sorted according to user, department, and user role. Upon final sign-off, a purchase
order is created through the system. The application only allows this transaction to occur once
the RTP has been approved. Similar to the RTP process, additional modules follow the same security
protocol, though to a lesser degree.
If the user finds sufficient materials in stock, he can logon to the Stock Requisition Slip (SRS)
portion of the application and initiate processing; the requested materials are filtered through
a dropdown list based on dynamic allotment by department. This is determined the department's
inventory and usage.
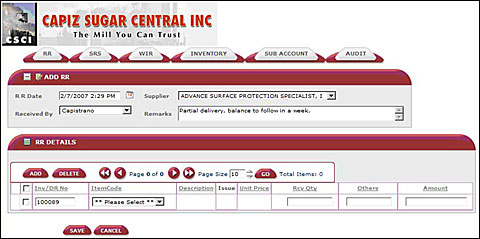
Items ordered by the selected supplier populate each dropdown list.
|
Application size and scope |
The application uses one Microsoft SQL 2000 database with over 30 tables. There are
over 86 web pages accessed by 100 users who process approximately 2,000 transactions
per month. The largest database table is the Inventory table, containing approximately
5,000 records at the time of this writing. The RTP master and detail tables are also about
5,000 records, and the number of records in these tables will likely double each year.
|
The project |
The Request to Purchase and Purchase Order modules were implemented in about 60
person-days over three months. I developed and released succeeding modules about every
month thereafter, updating them from time to time to incorporate new features. I have
also migrated the applications to new releases of Iron Speed Designer to take advantage
of new functionality in the tool.
I developed the entire application on my own, with graphic design and testing help.
Each application module took no more than one day to create. I spent extra time customizing
and testing the application in order to incorporate the appropriate business logic.
|
Code extensions and customizations |
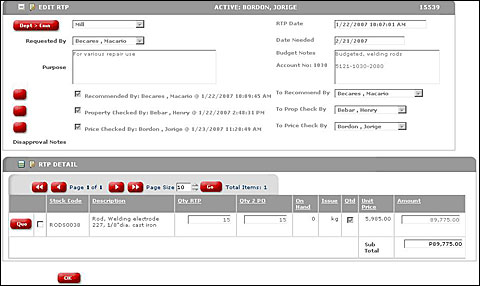
Action buttons are hidden or disabled once a document has been approved or disapproved.
The major customizations include:
 | Password security.
|
 | Custom saving routine for complete control of administrative processes.
|
 | Dropdown list customizations. 90% of the dropdown boxes were customized to include filters based on planned sources within the table panels. The new fields incorporate a dropdown list loaded with the filtered data, while the existing fields remain hidden without the large list selector control. This value is replaced with literals in the form of show fields.
|
 | Validation tags.
|
 | Email workflows.
|
 | Custom stored procedures.
|
 | Duplicate entry detection.
|
An error message is displayed intercepting multiple entries.
We also incorporated Crystal Reports, a third-party reporting tool, into this application
utilizing single and multiple parameters.
To increase efficiency, all Page Load and Pre-render events are pre-loaded. These events
are populated with pre-planned values. Using hidden ASPX labels rather than session variables
reduces each view state and improves performance.
|
Layout customizations |
I modified the page layout minimally in order to increase visibility, making the data
easier to understand. These customizations included:
 | Reducing page size.
|
 | Removing redundant built-in buttons.
|
 | Increasing the number of columns on a page.
|
 | Altering several display types.
|
 | Incorporating custom buttons.
|
 | Integrating an export-to-PDF button.
|
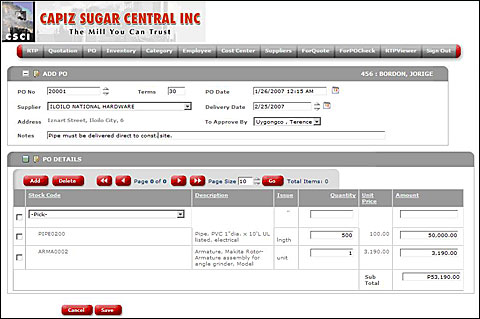
Web page size is kept to a minimum by populating dropdown lists on one new line at a time.
|
Iron Speed Designer impact |
The Material and Spare Parts Acquisition and Inventory Control System is my first
.NET web application. This is a quantum leap from the desktop development world
that I was used to. Iron Speed Designer allowed me to transition gracefully into
the .NET web development. It has also taught me how to develop in C#. The code and
stored procedures scripts in Iron Speed Designer application are a real-time learning
medium, offering interactive testing.
I saved well over 100 days of development time using Iron Speed Designer. This project
would not have been possible on my own. As a .NET web developer you must have a tool
that is versatile and highly dependable. Iron Speed Designer has allowed me to deliver
high-quality jobs beyond even my own expectations in every situation.
|
Next steps |
Phase two will commence as soon as the initial application becomes established in the
organization. Many of the code customizations will be reused in the next phase.
|
About the developer |
Jaime Jegonia
IT Consultant and Owner
JimiTron Software
Jaime is a Chemical Engineer by training and a .NET web developer by avocation.
His passion for development has transformed him into an Information Technology
Consultant and owner of JimiTron Software.
Jaime holds a degree in Chemical Engineering from the University of San Agustin
of Iloilo City, Philippines.
|
|
|
|
|